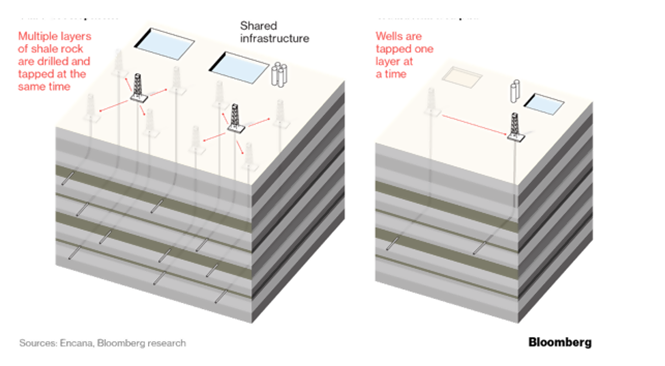
- In pad development many wells are drilled at the same time and later they are hydraulically fractured in groups.
- Lack of adequate characterization leads to cookie-cutter design approach which reduces profitability.
- Problems with frack hits and poor spacing become evident only
when they are put on production. - Wells are drilled out of zone, or with low net/gross
- Undulating well paths result to uneven drainage
- In infill pads there is parent/child interference
- After the pad is producing, there are not many options available to mitigate these problems, or to improve overall performance
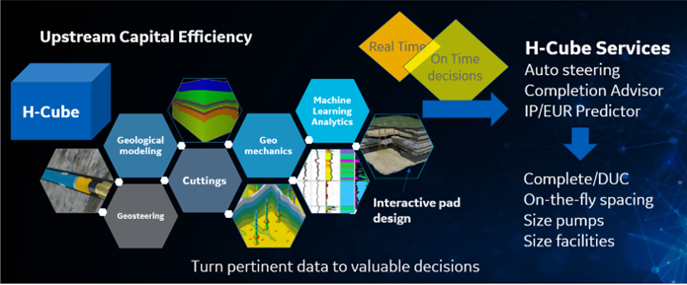
Solution:
- Offer interactive pad development solution (H-Cube)
- Provide subsurface integration to support on time decisions that will allow for interactive, information-driven resource development. Leverage proprietary data and software to enhance Capital efficiency and to improve performance metrics.
- Offer what operators are lacking:
- On-time subsurface characterization
- Adoptive well placement (as opposed to cookie-cutter plans)
- Informed hydraulic fracturing design
- Predictive capabilities based on early characterization
- Cost/benefit analysis at early pad construction stages to identify efficient low cost solutions
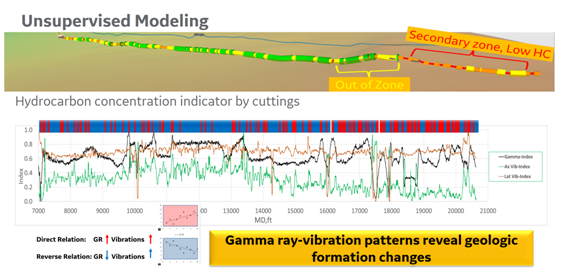
All subsurface information is integrated in 3D mapping in the JewelSuite platform which is also used to design hydraulic stimulation and predict production performance using geomechanics-driven engineering. In this process, image (ImageTrak) and deep shear acoustic (XMac) logging offer a valuable input if they are available. Cuttings analysis provides a rich spatial representation of subsurface indicators related to hydrocarbon concentration, matrix permeability, mechanical strength and more which can be calibrated with core analysis or performance based modeling to represent the subsurface clarity that is necessary to provide a rock driven pad design.
This subsurface integration although it is not real time, it is conducted in very short time frame to be on time between drilling and completion operations. The solution is a fast subsurface integration process where early measurements such as cuttings and drilling vibrations are combined with known geological parameters to offer a high resolution geologic description that allows an on-time adaptation of well design. As the first wells are drilled their data can influence the placement, spacing and coverage of subsequent wells, while the completion design is re-examined and re-processed to avoid adverse production interference. This process takes advantage of modern cuttings analysis and drilling sensing equipment processed with machine learning techniques.